Acrylic product production process
Acrylic handicrafts often appear in our lives with the increase in quality and quantity and are widely used. But do you know how a complete acrylic product is produced? What is the process flow like? Next, JAYI Acrylic will tell you about the production process in detail. (Before I tell you about it, let me explain to you what types of acrylic raw materials are)
Types of acrylic raw materials
Raw material 1: acrylic sheet
Conventional sheet specifications: 1220*2440mm/1250*2500mm
Plate classification: cast plate / extruded plate (the maximum thickness of the extruded plate is 8mm)
Regular color of plate: transparent, black, white
Common thickness of plate:
Transparent: 1mm, 2mm, 3mm, 4mm, 5mm, 6mm, 8mm, 10mm, 12mm, 15mm, 18mm, 20mm, 25mm, 30mm, etc.
Black, White: 3mm, 5mm
The transparency of the acrylic transparent board can reach 93%, and the temperature resistance is 120 degrees.
Our products often use some special acrylic boards, such as pearl board, marble board, plywood board, frosted board, onion powder board, vertical grain board, etc. The specifications of these special boards are set by the merchants, and the price is higher than that of ordinary acrylic.
Acrylic transparent sheet suppliers usually have stock in stock, which can be delivered in 2-3 days, and 7-10 days after the color plate is confirmed. All color boards can be customized, and customers are required to provide color numbers or color boards. Each color board proofing is 300 yuan / each time, the color board can only provide A4 size.
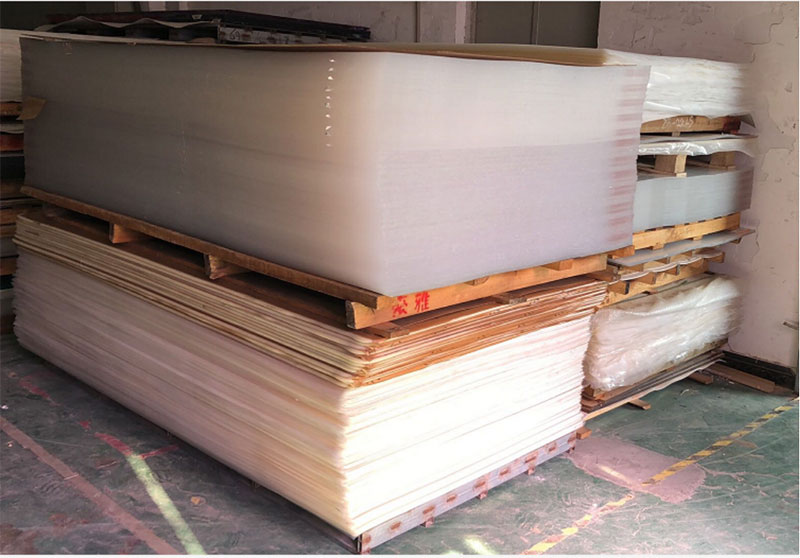
Raw material 2: acrylic lens
Acrylic lenses can be divided into single-sided mirrors, double-sided mirrors, and glued mirrors. The color can be divided into gold and silver. Silver lenses with a thickness of less than 4MM are conventional, you can order plates in advance, and they will arrive soon. The size is 1.22 meters * 1.83 meters. Lenses above 5MM are rarely used, and merchants will not stock them. The MOQ is high, 300-400 pieces.
Raw material 3: acrylic tube and acrylic rod
Acrylic tubes can be made from 8MM in diameter to 500mm in diameter. Tubes with the same diameter have different wall thicknesses. For example, for tubes with a diameter of 10, the wall thickness can be 1MM, 15MM, and 2MM. The length of the tube is 2 meters.
The acrylic bar can be made with a diameter of 2MM-200MM and a length of 2 meters. Acrylic rods and acrylic tubes are in high demand and can also be customized in color. The custom-made acrylic material can generally be picked up within 7 days after the confirmation.
Acrylic product production process
1. Opening
The production department receives the production orders and production drawings of acrylic products. First of all, make a production order, decompose all the types of plates to be used in the order, and the amount of plate quantity, and make a production BOM table. All the production processes used in the production must be decomposed in detail.
Then use the cutting machine to cut the acrylic sheet. This is to accurately decompose the size of the acrylic product according to the previous, so as to accurately cut the material and avoid the waste of materials. At the same time, it is necessary to master the strength when cutting the material. If the strength is large, it will cause a big break on the edge of the cutting, which will increase the difficulty of the next process.
2. Carving
After the cutting is completed, the acrylic sheet is initially engraved according to the shape requirements of the acrylic product, and carved into different shapes.
3. Polishing
After cutting, carving, and punching, the edges are rough and easy to scratch the hand, so the polishing process is used to polish. It is also divided into diamond polishing, cloth wheel polishing, and fire polishing. Different polishing methods need to be selected according to the product. Please check the specific distinction method.
Diamond Polishing
Uses: Beautify products and improve the brightness of products. Easy to handle, handle straight cut notch on the edge. The maximum positive and negative tolerance is 0.2MM.
Advantages: easy to operate, save time, high efficiency. It can operate multiple machines at the same time and can handle the saw grains cut on the edge.
Disadvantages: Small size (the width of the size is less than 20MM) is not easy to handle.
Cloth Wheel Polishing
Uses: chemical products, improve the brightness of products. At the same time, it can also handle slight scratches and foreign objects.
Advantages: Easy to operate, small products are easier to handle.
Disadvantages: labor-intensive, large consumption of accessories (wax, cloth), bulky products are difficult to handle.
Fire Throw
Uses: Increase the brightness of the edge of the product, beautify the product, and do not scratch the edge of the product.
Advantages: The effect of handling the edge without scratching is very good, the brightness is very good, and the processing speed is fast
Disadvantages: Improper operation will cause surface bubbles, yellowing of materials, and burn marks.
4. Trimming
After cutting or engraving, the edge of the acrylic sheet is relatively rough, so acrylic trimming is performed to make the edge smooth and not scratch the hand.
5. Hot Bending
Acrylic can be turned into different shapes through hot bending, and it is also divided into local hot bending and overall hot bending in hot bending. For details, please refer to the introduction of the hot bending process of acrylic products.
6. Punch Holes
This process is based on the need for acrylic products. Some acrylic products have small round holes, such as the magnet hole on the photo frame, the hanging hole on the data frame, and the hole position of all products can be realized. A large screw hole and a drill will be used for this step.
7. Silk
This step is generally when customers need to display their own brand LOGO or slogan, they will choose silk screen, and silk screen generally adopts the method of monochrome screen printing.
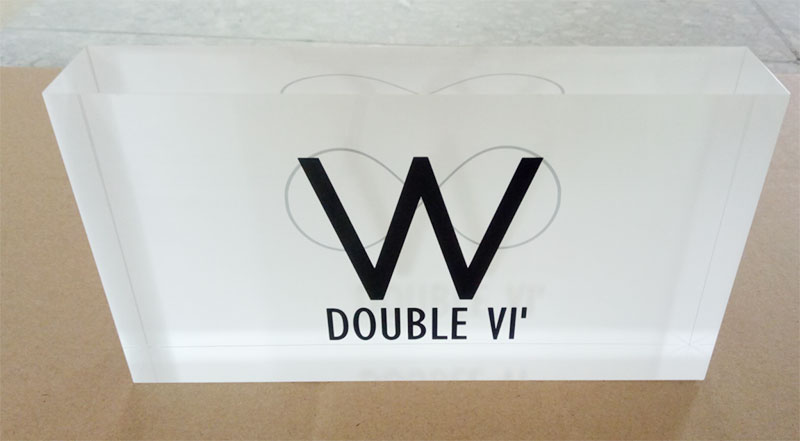
8. Tear Paper
The tear-off process is the processing step before the silk screen and hot-bending process, because the acrylic sheet will have a layer of protective paper after it leaves the factory, and the stickers pasted on the acrylic sheet must be torn off before screen printing and hot bending.
9. Bonding and Packaging
These two steps are the last two steps in the acrylic product process, which complete the assembly of the entire acrylic product part and the packaging before leaving the factory.
Summarize
The above is the production process of acrylic products. I don’t know if you still have any questions after reading it. If so, please feel free to consult us.
JAYI Acrylic is the world's leading acrylic custom products factory. For 19 years, we have cooperated with big and small brands all over the world to produce customized wholesale acrylic products, and we have rich experience in product customization. All of our acrylic products can be tested according to customer requirements (eg: ROHS environmental protection index; food grade testing; California 65 testing, etc.). Meanwhile: We have SGS, TUV, BSCI, SEDEX, CTI, OMGA, and UL certifications for our acrylic storage acrylic box distributors and acrylic display stand suppliers around the world.
Related Products
Post time: May-24-2022