Acrylic tray is a kind of tray type widely used in all walks of life. Its unique transparency, durability, and customizability make it popular in the market. The acrylic tray customization market demand is growing. Different industries and applications have their own requirements for the size, shape, function, and quality of trays. Traditional standardized trays cannot fully meet these requirements, so the customization of acrylic trays becomes more and more important. Through the customization of acrylic trays, enterprises can obtain tray solutions that match their products, operation processes, and brand image, improve logistics efficiency, reduce losses, and show a professional image.
The topic of this article is the acrylic tray customization process. We will introduce the various stages and links of acrylic tray customization in detail, including demand analysis and communication, design stage, material selection and processing, production and assembly, etc. By taking a deeper look at these processes, readers will learn how to customize high-quality acrylic trays to individual needs.
Next, we will explore the process of acrylic tray customization in depth to help readers better understand and apply knowledge in this professional field.
Acrylic Tray Custom Process
A) Requirement Analysis and Communication
In the process of acrylic tray customization, demand analysis, and communication are very critical steps. It involves effective communication and understanding between customers and acrylic tray manufacturers to ensure a comprehensive understanding and accurate grasp of customer needs.
Communication process between customer and manufacturer:
Initial Consultation
Customers first contact the manufacturer to express their needs and intentions for acrylic tray customization. This can be done by phone, email, or face-to-face meetings.
Requirement Discussion
The manufacturer conducts a detailed requirement discussion with the customer to understand the customer's specific requirements, including requirements in terms of size, shape, function, quantity, delivery time, etc.
Technical Advice
Manufacturers provide professional technical advice according to the needs of customers, including the selection of acrylic materials, the feasibility of the design, and other aspects of the proposal.
Quotation and Contract
The manufacturer provides a detailed quotation based on the customer's needs and discussion results and reaches a contractual agreement with the customer.
In the demand analysis and communication stage, acrylic manufacturers need to actively listen to the needs of customers, put forward professional suggestions, and maintain timely communication and feedback. A comprehensive understanding and accurate grasp of customer needs will lay a solid foundation for the subsequent design and production stages, ensuring that the final customized acrylic tray can fully meet customer expectations and requirements.
If you are in business, you may like
B) Design Phase
The design phase is a key step in the acrylic tray customization process, which involves formulating the specific design scheme of the acrylic tray according to customer needs and technical requirements. The following are the key steps and processes in the design phase:
1. Preliminary Design:
- According to the requirements and technical specifications provided by the customer, the tray manufacturer carries out the preliminary design. This includes determining the size, shape, appearance, and other basic elements of the acrylic tray, and drawing preliminary design drawings.
- Consider the use environment and requirements of the tray, such as load-bearing capacity, stacking mode, handling mode, etc., to ensure the implementation and practicality of the design.
2. 3D Modeling and Visualization:
- Using computer-aided design software, 3D modeling is carried out, and the preliminary design is transformed into a specific 3D model. So I can show better appearance and structure of the tray, and help customers to better understand the appearance of the end product.
- Manufacturers can utilize 3D models for visual presentation so that customers can review the design and suggest modifications. This helps ensure that the design aligns with the expectations and requirements of the customer.
3. Consider Size, Shape, and Function:
- In the design phase, the manufacturer needs to consider the size, shape, and function of the tray. The size should meet customer needs and practical application requirements, the shape should be suitable for the product and easy to handle and stack, and the function should meet the use purpose and special requirements of the tray.
- Details such as edge handling, load-bearing structure, and anti-slip design of trays should also be considered to ensure the stability, durability, and safety of trays.
4. Revise and Confirm Repeatedly:
- According to the customer's feedback and opinions, manufacturers make the necessary changes and adjustments, until the final design scheme to get customer recognition and satisfaction.
- This may require multiple communications and modifications to ensure that the design is exactly in line with the customer's expectations and that the feasibility and cost factors of actual manufacturing are fully taken into account.
The importance of the acrylic tray design phase can not be ignored. By considering size, shape, and function together, manufacturers are able to design customized acrylic trays that meet customer needs. Carefully designed trays can improve logistics efficiency, reduce loss, and enhance the brand image. Therefore, it is necessary to pay attention to details in the design phase to ensure the rationality and feasibility of the design scheme to achieve the best customization effect.
C) Material Selection and Processing
Material selection and processing is an important part of the acrylic tray customization process, which involves the selection of suitable acrylic materials and the corresponding processing and production. Here's the relevant information:
1. The Characteristics and Selection Considerations of Acrylic Materials:
- Transparency: Acrylic has excellent transparency, making it an ideal material for displaying and displaying products.
- Durability: Acrylic has high resistance to impact and wear, and can withstand greater pressure and use in logistics and warehousing environments.
- Light weight: Compared with glass, the acrylic material is light and easy to handle and operate.
-
Customizable: Acrylic can be flexibly processed and customized to meet the needs of different shapes and sizes through processes such as thermoforming, cutting, drilling, and so on.
- Dustproof and anti-static: Acrylic trays can have dustproof and anti-static characteristics to protect the product from dust and static electricity.
When choosing acrylic materials, the following factors should be considered:
- The use environment and requirements of the tray, including temperature, humidity, chemical contact, etc.
- Load-bearing capacity and durability requirements of trays.
- Customer's budget and cost constraints.
2. Acrylic Tray Processing Process and Technology:
- Cutting and molding: According to the design drawings, the acrylic sheet is cut into the desired shape and size using a cutting machine or laser cutting technology.
- Thermoforming: By heating and shaping, the cut acrylic sheet is formed into the specific shape of the tray. This can be done with a heat gun, hot plate, or vacuum-forming equipment.
- Processing of holes and slots: Using a drilling machine or laser cutting technology, the holes and slots are processed on the acrylic plate to facilitate tray stacking, fixing, or other specific purposes.
-
Surface treatment: According to the requirements, the acrylic tray is polished, sanded, or other surface treatment to improve the appearance quality and touch.
The processing process needs to be operated by experienced technicians to ensure the processing quality and accuracy of the acrylic tray. At the same time, safety measures should be paid attention to during processing to ensure the safety of operators and the normal operation of equipment.
With appropriate material selection and precise processing techniques, manufacturers can produce high-quality customized acrylic trays that meet customer needs. With excellent performance and reliability, these trays provide an effective solution for logistics and warehousing processes.
Welcome to our custom acrylic trays factory! We offer industry-leading customization services, so whether you need to customize your personal items or want to create a unique product for a corporate event, we can meet your needs. From design to production, our professional team will strive to create exclusive acrylic trays for you, so that you can feel a unique experience in every use.
D) Production and Assembly
The production process and technical details of acrylic trays are the key to ensuring the quality of the final product. Here's the relevant information:
1. Production Process and Technical Details:
- Prepare materials: Prepare the required acrylic sheets and other components according to the size and shape requirements determined by the design.
- Cutting and molding: Using a cutting machine or laser cutting technology, the acrylic sheet is cut according to the design requirements, and the thermoforming process is used to shape it into the shape of a tray.
- Machining holes and slots: Using a drilling machine or laser cutting technology, the holes and slots are processed in the acrylic sheet for tray stacking, fixing, or other specific purposes.
- Surface treatment: Polishing, sanding or other surface treatment of the acrylic plate to improve the appearance quality and touch.
- Assembly: According to the design requirements, the acrylic plate and other components are assembled, such as connection angles, fixing screws, etc., to ensure the structural stability and functional integrity of the tray.
2. Quality Control and Assembly Inspection:
-
In the production process, quality control is crucial. Manufacturers should set up strict quality control standards and conduct inspections and tests to ensure the quality and accuracy of each production link.
- In the cutting and forming stage, it is necessary to ensure that the size, shape, and Angle of the acrylic sheet meet the design requirements to avoid size deviation or bad deformation.
- When machining holes and slots, check whether their position and size are accurate, and ensure the smoothness and consistency of the holes and slots.
-
In the surface treatment stage, adequate polishing and sanding are carried out to ensure that the surface of the tray is smooth and scratch free, and any dust or dirt is removed.
-
In the assembly process, the fit and connection stability of each component should be carefully checked to ensure that the structure of the tray is firm and functional.
Through strict quality control and assembly inspection, manufacturers can ensure that no quality problems or defects occur during the production of acrylic trays. This helps to provide high-quality, reliable tray products that meet customer needs and ensure reliability and durability in logistics and warehousing environments.
Custom Acrylic Tray Case
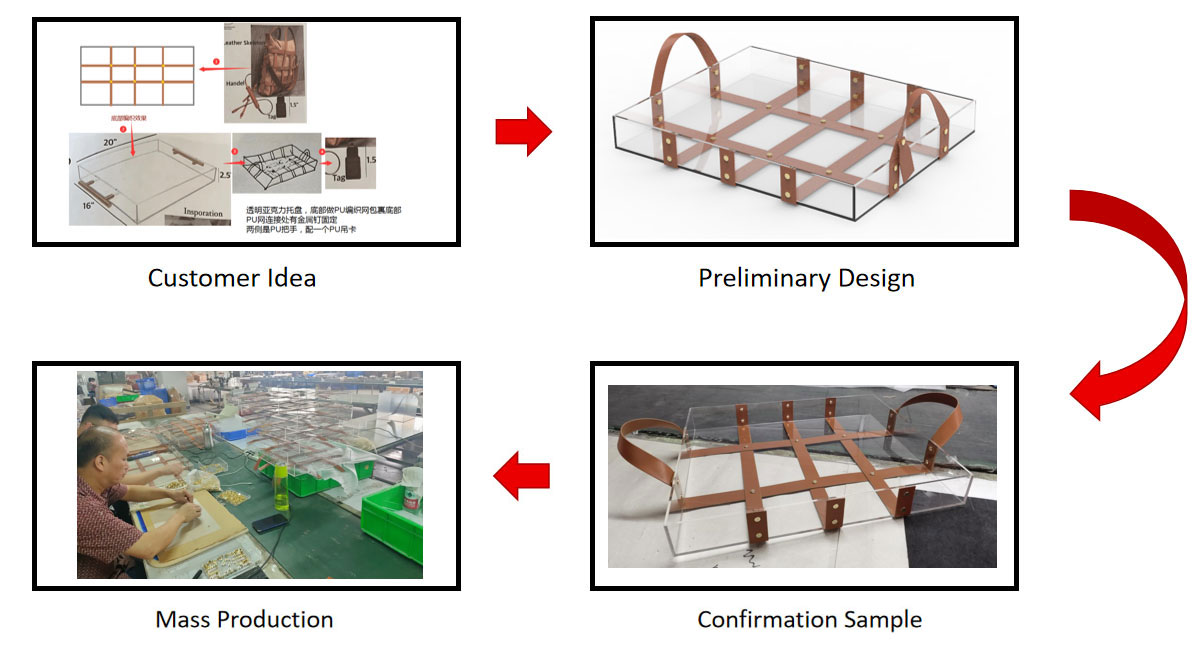
Summary
This paper discusses the fabrication and assembly process of acrylic trays, emphasizing the importance of quality control and assembly inspection during the fabrication process. Through strict quality control and assembly inspection, manufacturers can ensure that no quality problems or defects occur during the production of acrylic trays, thus providing high-quality and reliable tray products.
The Acrylic Tray Customization Process has the Following Advantages:
- Customization: Acrylic trays can be customized according to customer needs and requirements, including size, shape, function, and appearance. This enables acrylic trays to meet the specific needs of different industries and applications, providing personalized solutions.
- Lightweight and Durable: Acrylic material has a low density, making acrylic trays relatively light, and easy to handle and operate. At the same time, acrylic material also has excellent durability and can withstand heavy loads and impact resistance, ensuring the long-term use of trays in logistics and storage environments.
- Transparency and display effect: Acrylic tray has good transparency, can clearly display products, improve the display effect and attractiveness of products. This is particularly important for retailers and the display industry to effectively attract the attention of consumers.
- Anti-static and dustproof performance: acrylic material can be treated with anti-static to avoid damage to products and electronic components caused by electrostatic interference. In addition, the smooth surface of the acrylic tray also reduces the accumulation of dust and dirt, maintaining the cleanliness of the product.
The Acrylic Tray Customization Process has Broad Market Prospects:
- Logistics and warehousing industry: Acrylic trays are widely used in the logistics and warehousing industry, which can improve the transportation efficiency and storage management of goods. With the growth of global logistics demand, the market demand for acrylic trays will continue to increase.
- Retail and display industry: Acrylic trays can provide a clear product display effect, making them widely used in the retail and display industry. With the increasing retail competition and consumers' emphasis on product appearance, the market demand for acrylic trays will continue to grow.
- Electronics and semiconductor industry: The anti-static properties of acrylic trays make them an ideal choice in the electronics and semiconductor industries. With the continuous development of electronic products and the increase in demand, acrylic trays in the industry market prospects are very broad.
To sum up, the acrylic tray customization process has many advantages and has broad market prospects in logistics, warehousing, retail, display, electronics, and semiconductor industries. Manufacturers can meet customer needs through professional production processes and quality control, and provide high-quality, personalized acrylic tray products.
Post time: Aug-29-2023